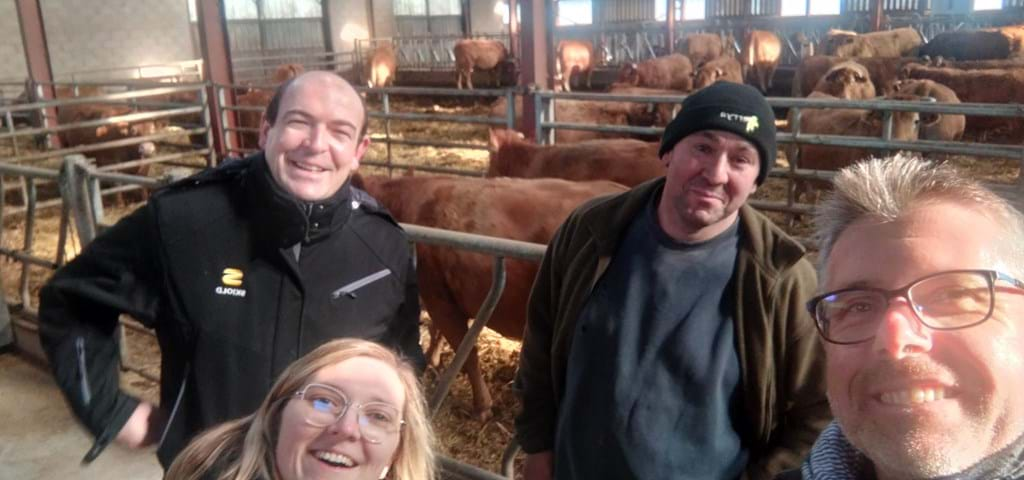
Now, the time we save is spent looking after the animals
Optimises feed efficiency by converting from crusher to SKIOLD Disc Mill.
In December 2021, we went to the southwest of France to meet with breeders who produce their own feed. The objective was to get their feedback on our SKIOLD feed mill solutions. Beginning the Aveyron journey, we started at an altitude of 900 m to meet Jérôme, from GAEC Saint Jean Le Froid, and breeder of the Label Rouge & IGP Veau d'Aveyron and Ségala sector.
Label Rouge & IGP Veau d'Aveyron et du Ségala.
From crusher to a global solution
Originally, Jérôme and Geneviève wanted to replace their crusher. To do this, they contacted the installer closest to the farm, Agritech Elevage, which is 30 minutes away and is a leading installer in Aveyron.
Sylvain Lagarrigue, technical sales representative at Agritech Elevage, advised them to go for a grinding and feed distribution system.
"We had recently expanded the building. So, when we multiplied the distance from the building by 2 and we had to go 80 m with the wheelbarrow, it was funny. We had a click. While we only wanted to change the crusher, Sylvain directed us to this system that manufactures and distributes the feed. And that's very good," Jerome said.
Ultimately, the objectives were:
- Automate to reduce arduousness and save time,
- Homogenize the mixture (1/3 complementary and 2/3 cereals) for the calves.
From manual to automated management
After the beginning of the project, a first meeting took place before the confirmation. "We thought about the technical solution that we were going to propose, present and validate to the customer for 6 months. " says SKIOLD National Sales Director in France, Eric Manenc.
"Initially, we had to start with manual valves. Starting from nothing to turning turn valves was already quite something. And in fact, there was no big difference in price to make the solution automatic. At least there was no more touching. Finally, we went with automated valves to make it easier for my wife who distributed the feed and to gain precision in terms of mixing," the customer says.
In addition, the visit to a farm with automated distribution by flexible augers made it possible to make choices in the construction of the project.
"Each project is unique. The technology may be the same but the environment around it is different. You have to adapt the technology to the existing environment", Eric Manenc explains.
A simple and reliable automated system
Approved in December 2020, the scalable solution includes:
- handling,
- storage,
- automation - SKIOLD Fabristar S
- a factory core consisting of a Disc Mill and a 1200 L vertical mixer and transfer by chain from feed to feeders (calves) and hoppers (cattle).
"In fact, the interesting point in this project is the distribution of dry feed automated by the Fabristar S, a feed manufacturing machine that we have optimized to ensure distribution. Thus, we have 2 possibilities:
- Fill a classic silo
- Distribute
Since the feed mill is located next to the cattle building, we used a chain distribution system to the calf feeders and cattle hoppers. The feeders are equipped with sensors that show the system if the feeders are full or not. We have automated tees for groups of feeders", Sylvain Lagarrigue explains.
Today, the distribution system includes:
- 2 formulas (1 for cattle with a nitrogen corrector / 1 for calves)
- 7 delivery points
For calves: 4 feeders with the same formula (opening of all 4 tees simultaneously)
For cattle: each hopper has its own formula
- Suckler
- Pregnant
In conclusion, Sylvain Lagarrigue specifies that "the proposed equipment is reliable. For the tonnage to pass, 100 tons / year, the first maintenance will be several years from now. It is still necessary to check the magnet box from time to time. But this is a minor maintenance job. “
Time saved is spent on looking after the animals
"It used to be a lot of manual work. You had to transport the grain, which was in another building, to the crusher and then wait for the grain to pass through it. It took 3 hours a week to prepare a hopper that was consumed in a week. It was necessary to monitor the hopper on the crusher that had to be filled (800 kgs) on a regular basis. Once the hopper was filled, the telescopic device was used and the feed was distributed to the calves with a wheelbarrow. Then the nitrogen corrector was switched from the silo to the wheelbarrow. Finally, we went with the wheelbarrow in the corridors to distribute feed to the animals. Before, it took 45 minutes to distribute in the evening without counting the manufacturing time. Today, the time devoted to the feed production is 5 to 10 minutes in the evening before returning. For the calves, it is automated. For the cattle, it is different because I give them from the bucket. I check to see if the hopper is empty. If this is the case, I schedule the manufacturing for the next morning to have a fresh feed, ready to use in the hoppers", the breeder explains.
"It's made and delivered straight to the plate. It's fresh feed!" says Eric Manenc, who also stresses that "it is important to have a regular particle size. The finer the product, the better it is used by the rumen. This optimises feed efficiency.
Note that there is a risk involved when distributing crushed products: The product crumbles during transport and becomes fine. Before, the product was preserved since it was handmade. With the disc mill, we will grind the product into something regular, much less fine, and we will prevent this problem."
By switching from a crusher to a disc mill, Jerome feared that the calves would stuff themselves. And finally, "in the dung, we find few grains. They serve themselves at will. Today, the particle size is set at 1.6."
Finally, he adds that "now, the time saved, we spend it looking after and monitoring the animals. In this season, the calves are fragile, especially when it comes to their lungs. We pay attention to the flu. And we must make sure that they eat."
We thank him warmly for his welcome and the time he used us.
Installation by SKIOLD France.
Do you want to make your own cattle feed? Contact us to find out more about our customisable feed milling solutions:
CONTACT US FOR FURTHER INFORMATION
Information on the farm:
Two partners
110 Limousine cattle
UAA 200 Ha including 30 Ha of cereals
Production: Veau d'Aveyron and Ségala Label Rouge & PGI
SKIOLD solution: Disc Mill , vertical mixer, auger, and Fabristar S automation.